In today's fast-paced world, convenience and efficiency play a vital role in the success of any product. When it comes to beverage packaging, plastic drink caps have become indispensable for their ability to provide a secure seal, prevent leakage, and offer ease of use. Behind the production of these essential caps lies an integral component known as the plastic drink cap mould. In this article, we will explore the significance of plastic drink cap moulds, their manufacturing process, and their impact on the beverage industry.
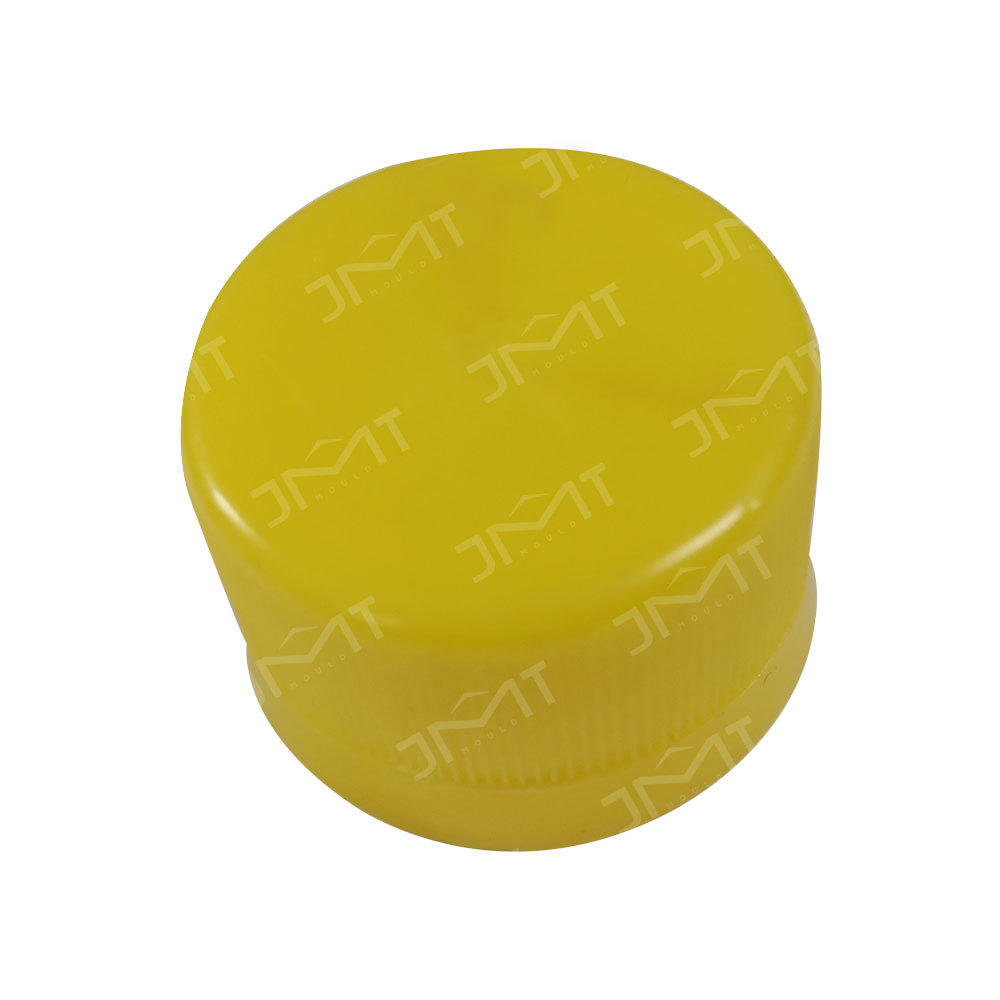
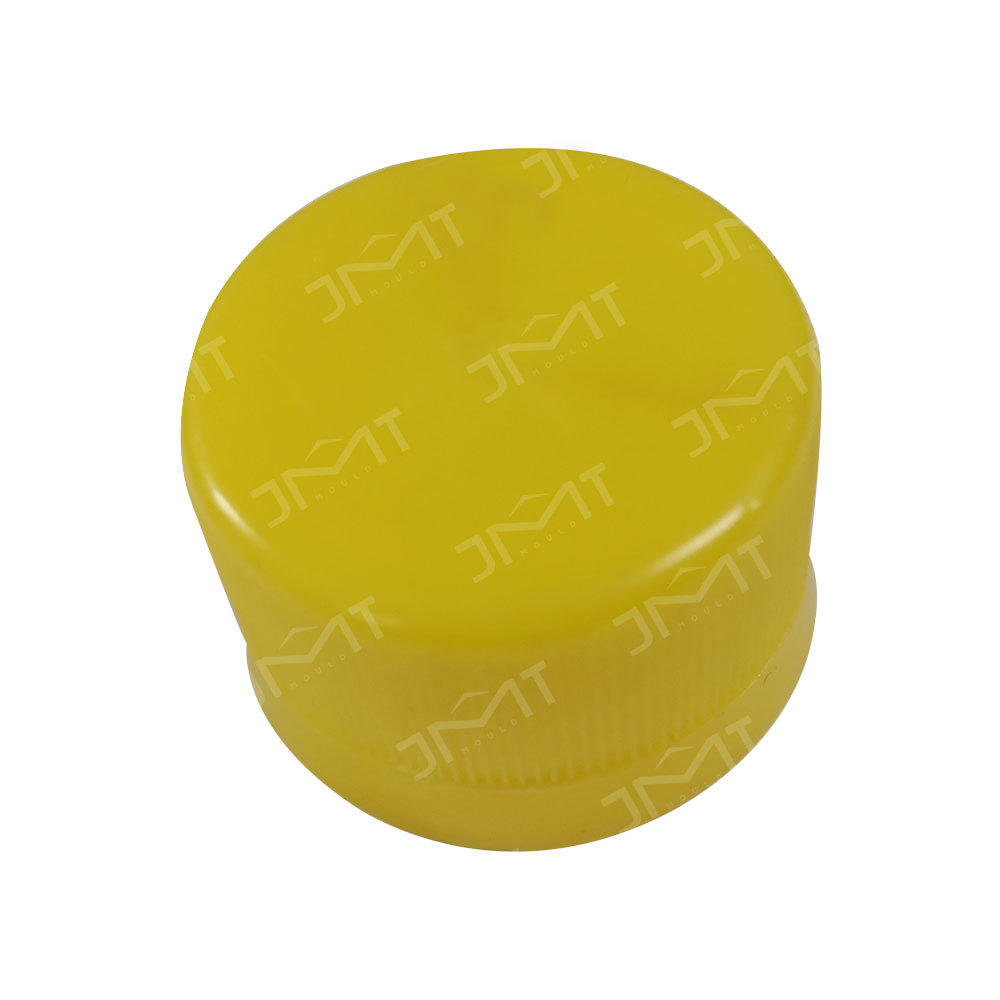
Understanding Plastic Drink Cap Moulds
A plastic drink cap mould is a specialized tool designed to shape and form plastic materials into precise and consistent cap designs. It consists of two halves, namely the core and the cavity, which fit together to create the desired cap shape. The mould is typically made of high-quality steel, ensuring durability and longevity. The intricate design of the mould allows for the formation of various cap sizes, shapes, and features, such as tamper-evident seals, spouts, and child-proof mechanisms.
Manufacturing Process
The manufacturing process of plastic drink cap moulds involves several steps, each crucial in achieving a high-quality final product. Let's take a closer look at the typical process:
Design and Prototyping: The initial phase involves conceptualizing the cap design and creating a 3D model using computer-aided design (CAD) software. Prototypes are then developed to validate the design before proceeding to production.
Material Selection: The choice of material for the mould is critical. High-grade steel, such as stainless or tool steel, is commonly used due to its durability, resistance to wear, and ability to withstand high production volumes.
Machining: Once the design is finalized, computer numerical control (CNC) machines are utilized to precisely shape the mould's core and cavity components. CNC machining ensures accuracy and consistency in the cap mould's dimensions and features.
Heat Treatment: After machining, the mould undergoes heat treatment to enhance its hardness, strength, and durability. This process involves carefully controlled heating and cooling cycles to achieve the desired material properties.
Finishing and Polishing: The mould undergoes a finishing process to remove any rough edges or imperfections. It is then polished to a mirror-like finish, which helps in the release of the formed caps from the mould.
Assembly and Testing: The core and cavity components are assembled, and the complete mould undergoes rigorous testing to ensure its functionality, accuracy, and longevity. This includes conducting sample production runs to verify the cap quality and consistency.
Impact on the Beverage Industry
Plastic drink cap moulds have had a significant impact on the beverage industry, revolutionizing the way beverages are packaged and consumed. Here are some key contributions:
Sealing and Protection: Plastic drink caps ensure a secure seal, preserving the freshness and quality of beverages while preventing leakage or spillage during transportation and storage.
Customization and Branding: Cap moulds allow for a wide range of customization options, enabling beverage manufacturers to create caps that align with their brand identity. This customization can include logo embossing, unique shapes, and color options.
Safety and Convenience: Cap moulds facilitate the inclusion of safety features such as tamper-evident seals, child-proof mechanisms, and spouts, enhancing consumer safety and convenience.
Production Efficiency: The use of cap moulds enables high-speed, automated production processes, increasing efficiency, and reducing production costs. This efficiency contributes to meeting the growing demand for beverages on a large scale.