A cap mould is the design of a bottle that will form a cap. These products are typically used in the beverage and food industry. A cap mould has a cavity that is open towards the core. The plastic is pushed through the hump on the core and expands as it expands to a groove. The angle of the groove varies depending on the design. A sharp angle would make it impossible to remove the plastic from the mould. The cap would act like a hook and shear off in the groove.
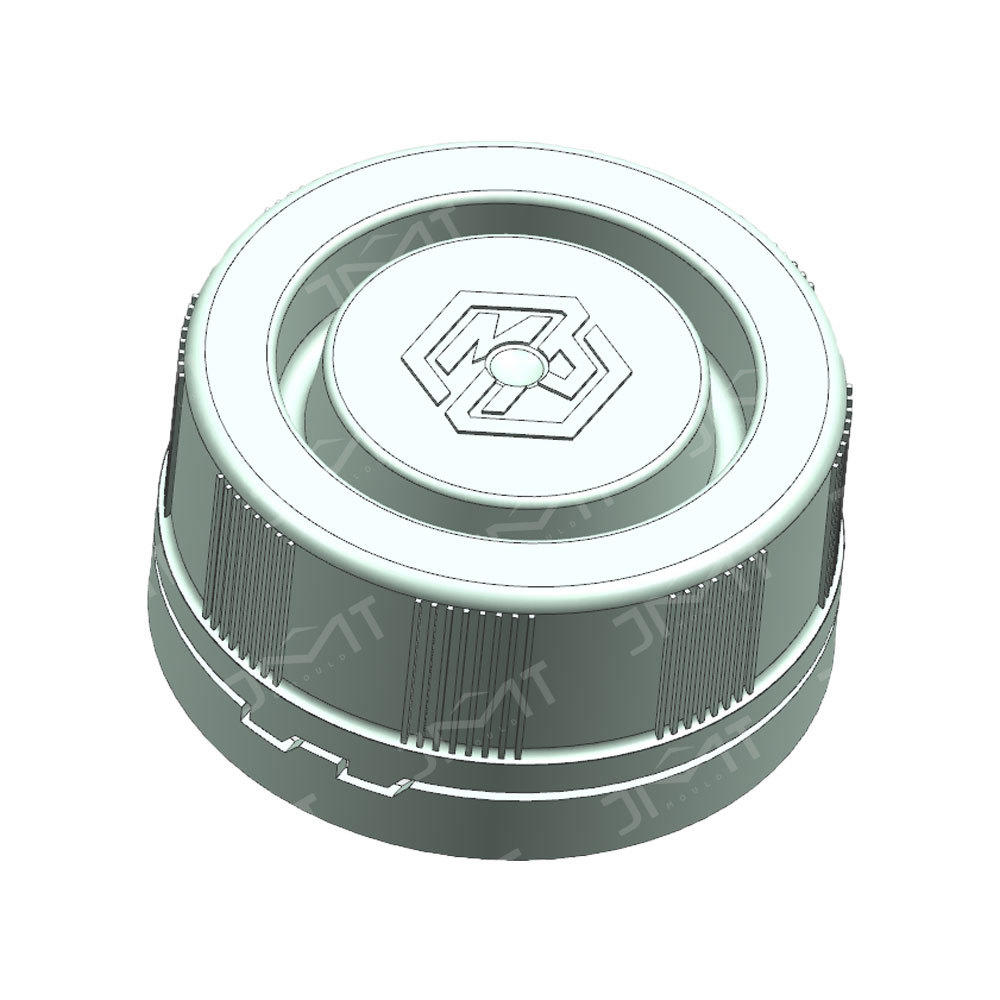
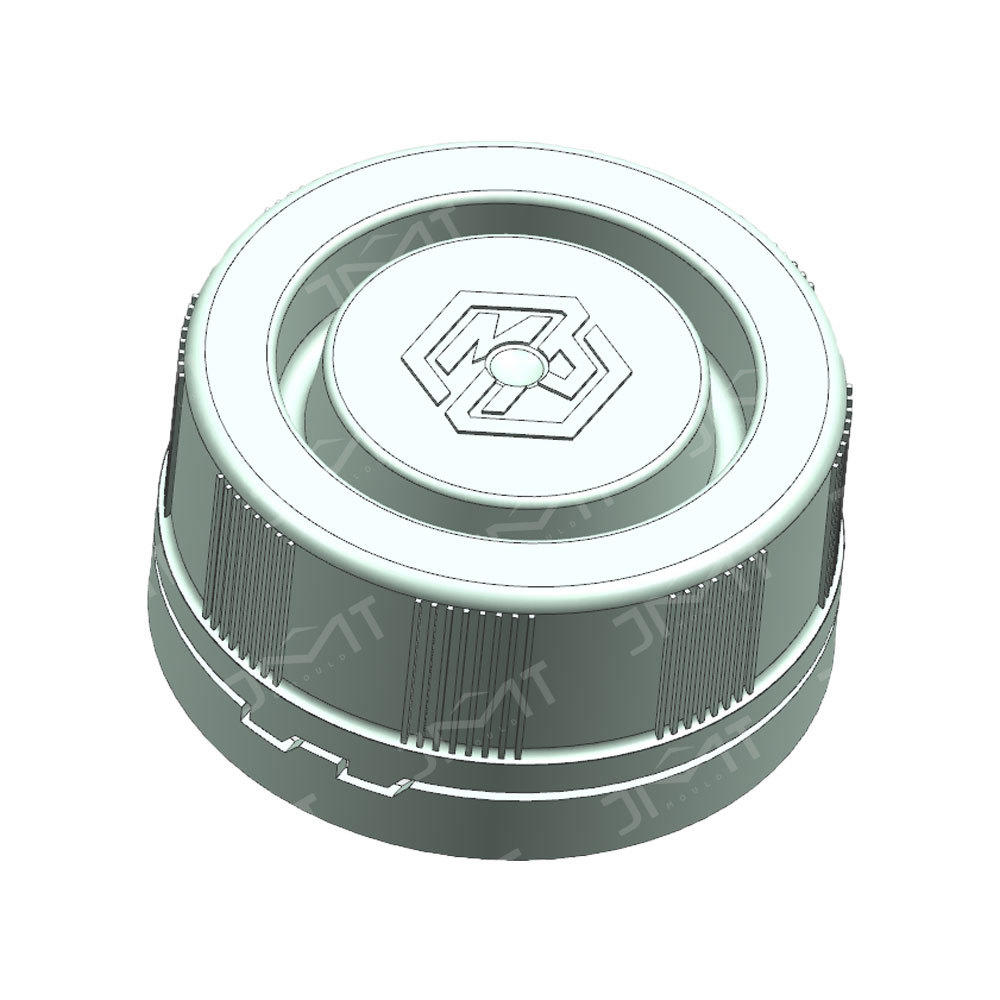
Threads are the next consideration. Some caps need to be unscrewed, while others need threading removed during production. A cap mould designed for unscrewing operations has multiple thread pitches, and needs a bigger actuating mechanism. Regardless of the type of product, it is important to have an accurate specification. It is important to know what the end-user needs from the cap mould, and the volume of product that they are trying to make.
Threading is another important consideration when designing a cap mould. There are two main methods: unscrewing and stripping. The former is more common and involves a higher degree of precision. If the threads are not uniform, then the end-product may not be symmetrical. In this case, a cap mould should be flexible enough to accommodate varying threading. The best way to get a standard cap mould is to choose one with multiple cavity options.
Threads are important to the design of a plastic cap mould. Threads must be easily removed from the core to avoid causing damage to the finished product. When designing a cap mould, it is important to consider the threading ability. There are a variety of reasons why stripping is easy, but in the end, the most important factor will be the size of the threads. Using a standard screw cap mould for unscrewing will allow you to produce many different types of caps and bottles.
A cap mould is very useful in the plastic beverage industry. A quality plastic cap mould will be easy to clean. Its high temperature will ensure a consistent product. The nozzles are essential for a smooth, reliable injection. They are vital to the overall quality of your product. They are also very important for preventing the cap from falling out. The right caps will not only make your customers happy, but will also make the world a safer place to live.
Molds are very important for the production of plastic products in large volumes. They can be expensive, but they can be useful for a wide range of applications. A cap mould is perfect for plastic bottles and can help you achieve your goals. Its durability is important for a high-quality product. Some cap moulds can be used for many different things, including ice cream and food. A mould is useful for a variety of applications, from car parts to surgical instruments. Whether you're making cosmetics, liquids, or other products, you'll have a cap mould that suits your needs.
The most important thing to consider when purchasing a cap mould is its size. You need to consider the number of cavities. For instance, a cap mould that has 32 cavities will have a higher cost than one with just eight. The mold will need to be larger than a cap mould made of smaller parts. The size of the cavity will determine how many bottles can be produced. Once you have a good number of caps, you can then decide what type of mould to use.
A cap mould is important for the production of high-volume plastic products. For example, it should be durable and economical. It should also be durable and can handle high-pressure plastic. Injection molding is popular for producing flexible products. But it can be expensive if you have a small mold. However, this method is beneficial if you want to produce a large volume of parts. A mould can be very durable. If it is built with steel and aluminium, it can produce a high volume of caps.
Choosing the right cap mould is important for a number of reasons. You will need to take into consideration the volume of plastic you need to produce. You should also consider the price of the mold. The cost of a cap mould depends on the volume of the product you need to make. Often the cost will depend on the number of cavities. A large mold can be made to fit a number of parts. Those with large cavities need a higher quality tool.