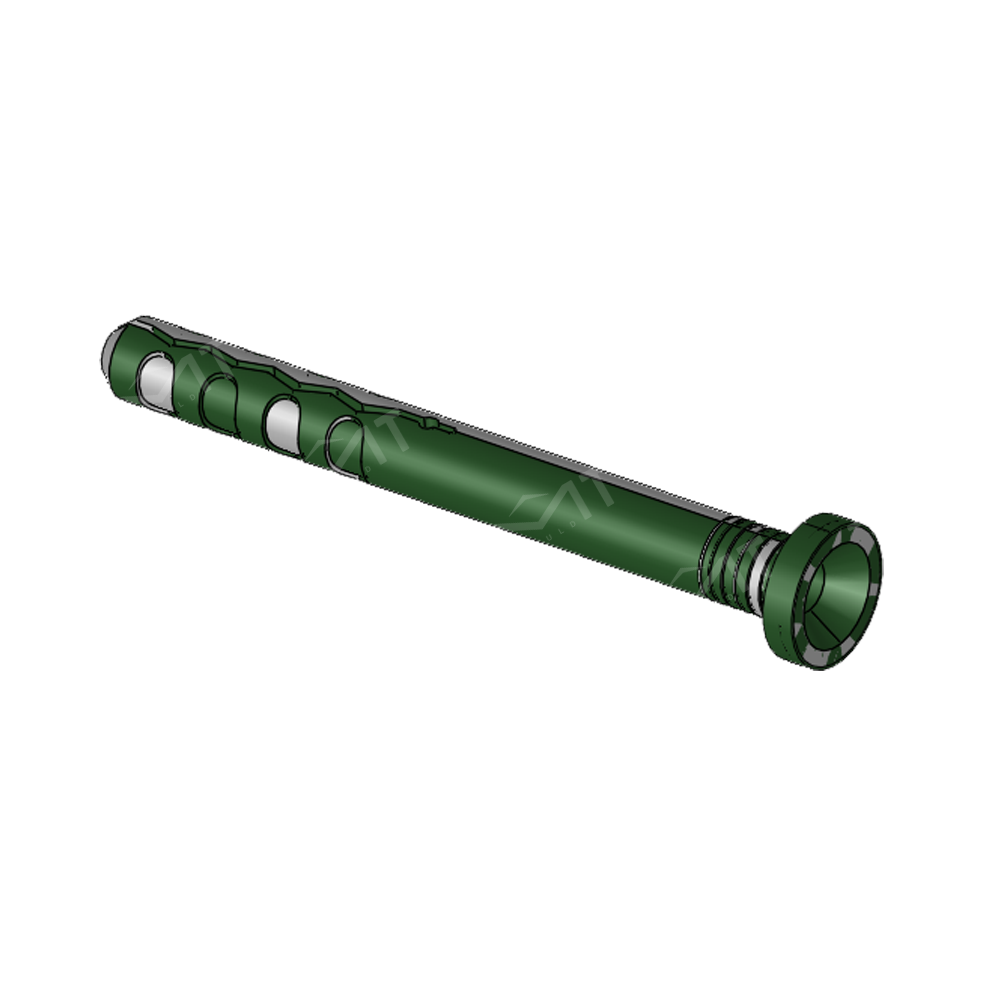
In this article, we will delve into the various types of plastic plug moulds, their key features, and the various applications they serve. We will also discuss the factors to consider when selecting a plastic plug mould and how to ensure the mould delivers high-quality plugs consistently.
Types of Plastic Plug Moulds
Plastic plug moulds come in various types, each designed to produce plugs of specific shapes and sizes. Some of the most common types of plastic plug moulds include:
Round Plug Moulds: As the name suggests, these moulds are used to create round plugs of various sizes. Round plugs are commonly used to seal electrical cables and prevent leaks in pipes.
Square Plug Moulds: These moulds are used to create square plugs that are used in applications where a tight seal is required. Square plugs are also used to fill holes in various surfaces, such as walls and floors.
Rectangular Plug Moulds: Rectangular plug moulds are used to produce plugs with a rectangular shape that can be used to seal openings in various systems and devices.
Custom Plug Moulds: If you have a specific shape or size in mind, you can opt for custom plug moulds that are tailored to your requirements.
Key Features of Plastic Plug Moulds
Plastic plug moulds come with a range of key features that contribute to their efficiency and durability. Some of the key features to consider include:
Material: Plastic plug moulds are typically made from high-quality materials such as aluminium or steel, which are known for their durability and resistance to wear and tear.
Cavity: The cavity is the space within the mould where the plastic is injected and shaped into the desired plug. The size and shape of the cavity will depend on the size and shape of the plugs you want to produce.
Runner System: The runner system is the pathway through which the molten plastic is injected into the cavity. The runner system should be designed to ensure a smooth flow of plastic and minimize waste.
Ejector System: The ejector system is responsible for pushing the finished plugs out of the mould once they have cooled and hardened. The ejector system should be strong and reliable to ensure the plugs are ejected smoothly without damage.
Cooling System: The cooling system helps to cool the molten plastic as it is injected into the cavity, ensuring the plugs harden evenly and consistently.
Applications of Plastic Plug Moulds
Plastic plug moulds are used in a wide range of applications, including:
Electrical and Electronic Devices: Plastic plugs are commonly used in electrical and electronic devices to seal and protect electrical components and prevent short circuits.
Automotive Industry: Plastic plugs are used in the automotive industry to seal various components and prevent leaks in fuel and oil systems.
Construction: Plastic plugs are used in construction to fill holes and seal openings in various surfaces, such as walls and floors.
Medical Devices: Plastic plugs are used in medical devices to seal and protect various components and prevent leaks.
Packaging: Plastic plugs are used in packaging to seal containers and prevent leaks.