A thermoplastic raw material is fed into an injection mould through a hopper. The material is heated and then forced into the mould's cavity by a reciprocating screw. The screw forces the material forward, mixing and homogenising the viscous and thermal distributions of the plastic. Once enough material has accumulated in front of the screw, the injection process starts. Once enough material is deposited, the screw forces the molten plastic into the mould through the sprue.
Aside from the material used, an injection mould also features a cavity. The mould cavity is sized to fit the plastic as it cools from a liquid to a solid state. This allows the plastic to shrink back to its desired size. However, a good manufacturer will also provide an insert made of brass, which will be added to the plastic part. It is important to ensure that the plastic used in the mould is safe to use before the injection process begins.
Plastics are another popular material used in injection moulding. The process is useful for making engine components, cylinder head covers, oil gauges, and more. It also offers a wide variety of shapes and finishes, and has excellent insulating properties. Other products that are created by injection moulding include toys, portable potties, and jewel boxes. The process is also beneficial for the design of electronics, such as circuit boards. For more information about the process, visit the website of a plastics mould manufacturer
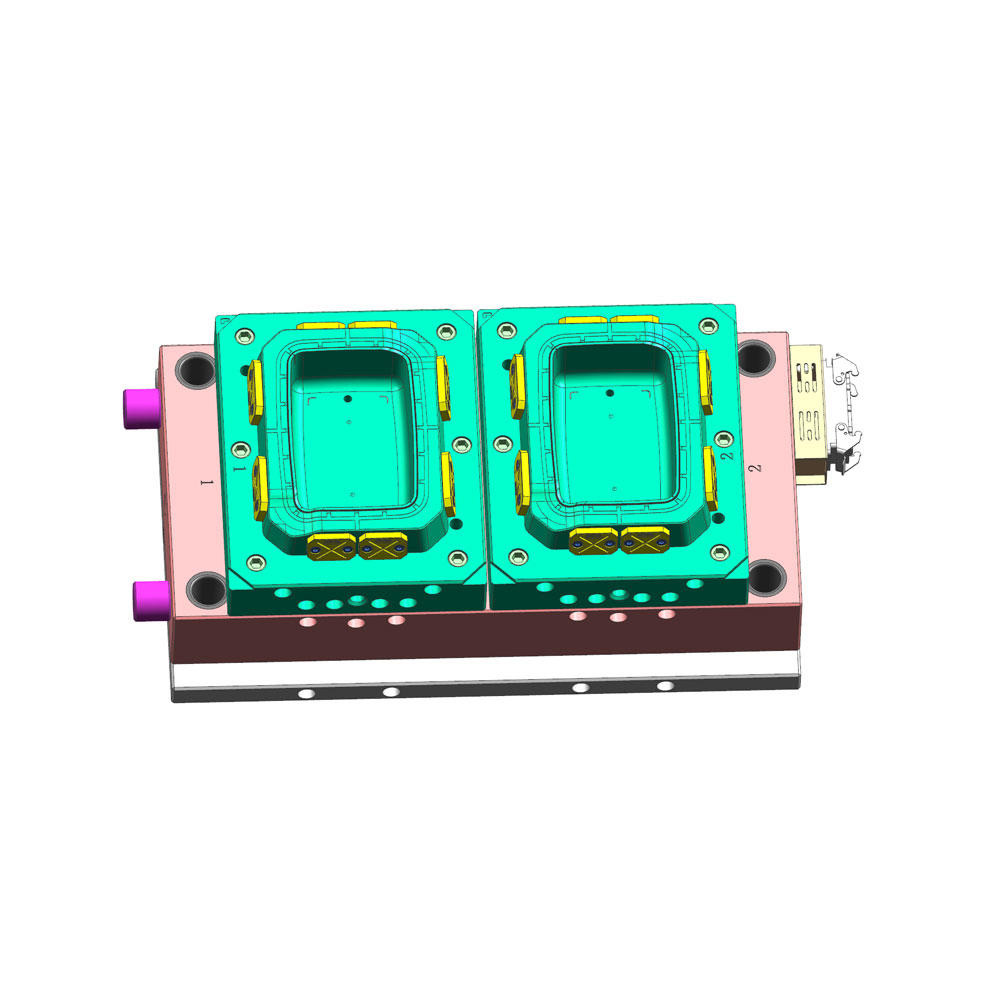
The cost of plastic injection moulding depends on several factors. The primary factors are the type of plastic compound, the complexity of the parts, anticipated quantities, and the size of the injection mould. The mould will also need to be designed to prevent sink marks. The tool will need to be designed with precision to minimise waste materials and encourage de-moulding. A high-quality injection mould will make durable products that last for years. A small amount of time and effort will save in the long run.
Injection moulding mistakes are costly and can affect the final product. These mistakes can be due to the materials used, or to the injection process itself. These defects range from harmless quality problems to safety hazards. While it may be difficult to detect the injection moulding defect, there are a few key signs that indicate it might be an issue. Listed below are some examples of defects and how to avoid them. When they occur, the quality of the final product is compromised.
Injection moulding processes produce material waste. This waste material has an impact on the environment, and must be recycled or disposed of appropriately. Modern injection moulding machinery consumes 20 to 50% less energy than those used just a decade ago. If you're looking to reduce your carbon footprint, the process is the perfect solution. For your plastic-injection moulding needs, consider these tips. They will help you reduce waste materials, while providing you with high-quality products.
During the injection moulding process, the material flow rate will determine the minimum wall thickness required. By ensuring the mould cavity is uniformly thick, you'll avoid short-shots and uneven surfaces. A thicker section will be cooled first, while a thinner one will be cooled afterward. When a thicker section is cooled first, it will shrink and contract the boundary area. The stress, however, can cause cracking and warping.
Before buying a plastic injection mould, it's important to determine how many parts you need to manufacture. Remember that the amount of products you'll be producing will ultimately depend on the type of mold you select. Make sure the material you're going to use will be compatible with the injection mould. If you're planning on producing a large number of items, you'll need to choose a multi-cavity mold. Using a thirty-two-cavity mould, for example, would result in a product of 34 million plastic components.
When building an injection mould, there are many different methods available. Standard machining, EDM, and CNC machining are the most common methods. These two techniques have different advantages. CNC machining allows for more intricate mould details, while standard machining is the traditional method for mould construction. Additionally, the more complex moulds can be produced faster and with greater accuracy. Another important factor in the cost of an injection mould is the number of cavities. The lower the number of cavities, the lower the tooling costs are. Additionally, surface finishes and additional details can influence the cost.
The cost of an injection mould can be very high. The initial set-up costs can be hundreds to thousands of pounds. However, if you need to make a large amount of parts, the cost can go up to $80,000 or more. A single cavity injection mould can cost up to $12,000, and a high-quality mould can cost up to $80,000 or more. Despite its high cost, the quality of the parts produced with injection moulding is very high.